Liquid Screed
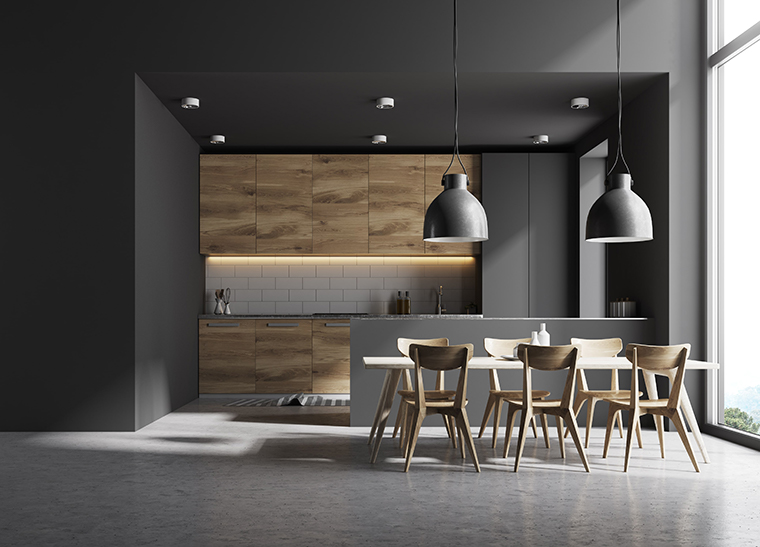
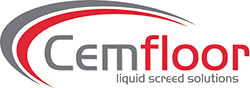
Cassidy Brothers supply liquid screed for commercial and residential projects in the North West of Ireland. The screed that we supply is Cemfloor which is produced to EN 13813:2002 requirements.
A high quality flowing floor screed can be produced simply by mixing with water either on site or at a ready mix plant. Flowing screeds have many obvious benefits over traditional sand and cement screed: quicker to lay; thinner screed depth; less labour intensive; much lower risk of shrinkage or cracking but the main benefits are seen when they are used with under floor heating ystems. Flowing anhydrite screeds fully encapsulate the heating pipes without voids and needs only to cover the pipes by 25mm, resulting in a much more responsive heating system which in turn is more economical to run.
Further reduced screed thickness enables maximised insulation, resulting in improved U-values.
Benefits over traditional sand and cement screeds:
- Quicker to lay
- Reduced drying out times
- Enables early start date for follow on trades
- Less labour intensive / improved health and safety benefits
- Thinner screed depth
- Produced from recycled and sustainable materials
- Maximises under floor heating performance
- Lower shrinkage
- Apply up to 1000m3 per day
- Maximise insulation thickness
- Reduced load bearing due to thinner screed depth